- Small teams will assemble key components before these parts are combined in the final assembly.
- Analysts say the new way of building a car could reduce manufacturing footprints by over 40%.
- Most mass-market cars still use the traditional assembly line pioneered by Henry Ford in 1913.
Tesla’s highly anticipated $25,000 electric vehicle won’t just be its most affordable model yet; it’s poised to introduce an innovative manufacturing approach that could dramatically slash costs.
The automaker refers to its new manufacturing approach as the ‘unboxed’ method. Instead of relying on a conventional assembly line, Tesla intends to deploy small teams of workers to simultaneously assemble different key components of the vehicle, which will then be integrated during final assembly. This innovative approach to car manufacturing holds the potential to halve production costs and shrink the required manufacturing footprint by over 40%
Read: Tesla Wants To Cut Manufacturing Costs In Half In Order To Build A $20k EV
Speaking about the unboxed approach late last year, Tesla’s vice president of vehicle engineering Lars Moravy said “if we’re going to scale the way we want to do, we have to rethink manufacturing again.”
Since Henry Ford invented the assembly line for the Model T in 1913, the vast majority of mass-market vehicles have been produced in this way. However, Tesla executives note this approach has many inefficiencies. For example, an entire vehicle is painted in this process whereas the unboxed method will allow Tesla to only paint those parts that need painting.
In January, Elon Musk said Tesla was “very far along” in the development of its new entry-level model and described its “revolutionary manufacturing system” as “far more advanced than any automotive manufacturing system in the world, by a significant margin.”
Engineering and automotive benchmarking firm Caresoft has told Bloomberg it has created a digital replica of Tesla’s unboxed platform. It says it is technically possible and could make “huge financial sense.” While some analysts believe Tesla could save up to 50% using this process, analysts from Bloomberg Intelligence think it could reduce manufacturing costs by roughly 33%.
For all the potential savings of the unboxed method, it remains unproven and will require Tesla to adopt a completely new assembly process which may cause delays. However, if Tesla achieves its targets, it could strengthen its stranglehold on the electric vehicle market.
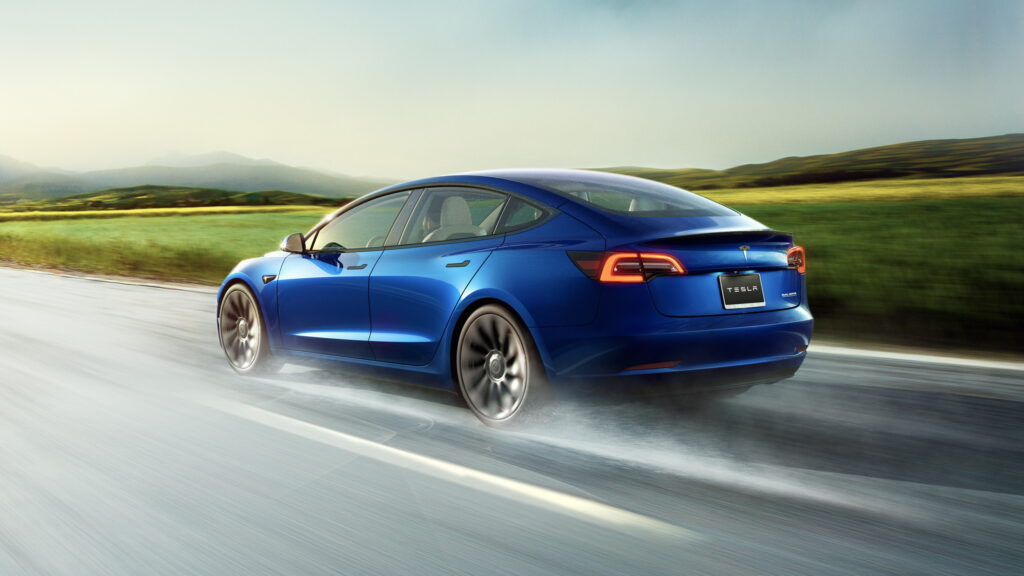